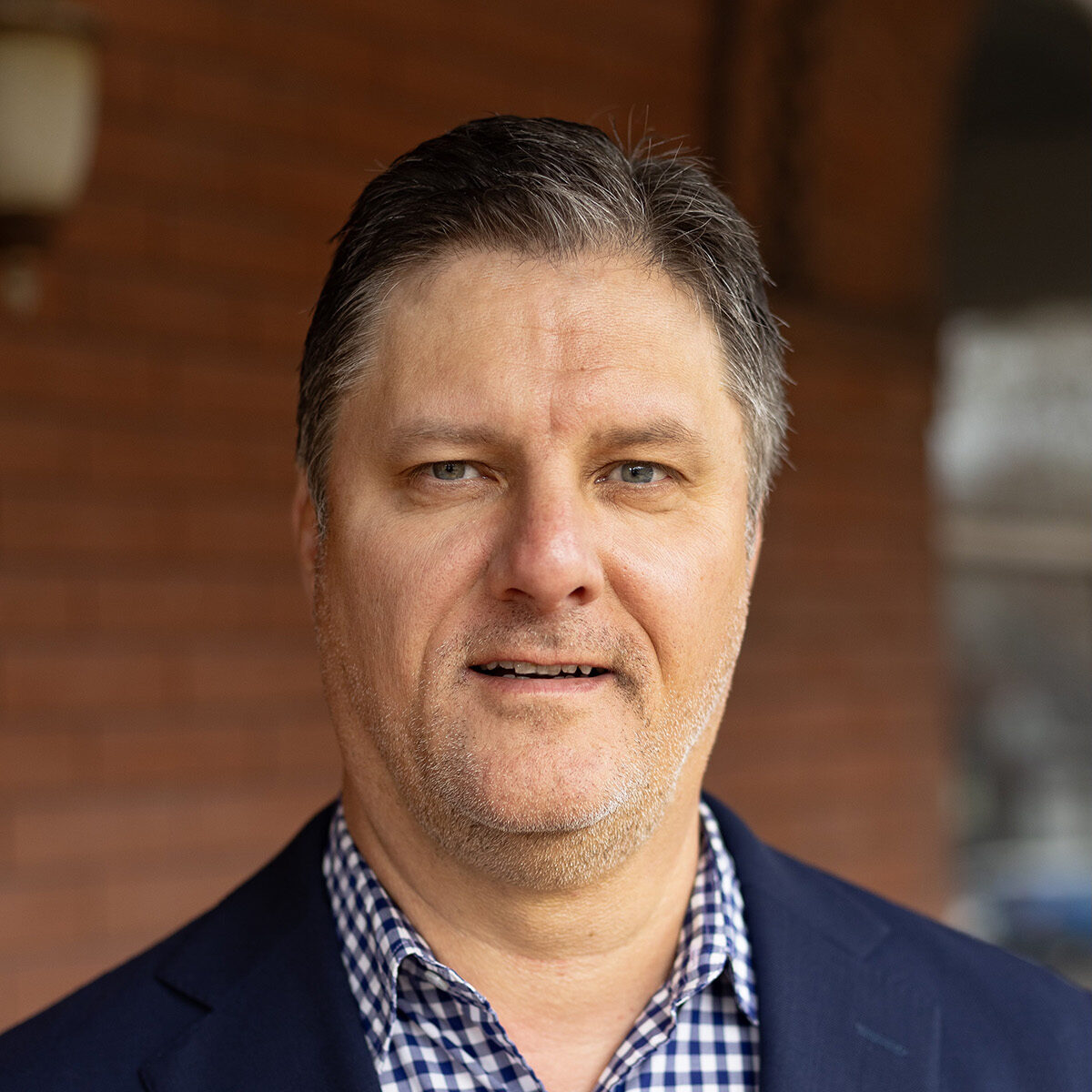
Josh Boggess
Vice President, Americas Channel Sales
Stratasys
The global manufacturing landscape is entering a new era—defined not just by technological change, but by a dramatic shift in economic and geopolitical realities. With new tariffs already in effect under the returning administration, the U.S. is actively pursuing a protectionist trade strategy, signaling a definitive break from decades of globalization. These tariffs, aimed at reducing dependency on foreign-made goods, are already impacting the cost and flow of products across borders. While some industries scramble to adapt, others are turning to a powerful enabler of resilience and agility: additive manufacturing (AM), commonly known as 3D printing.
At a time when manufacturers face rising costs, fragile logistics, and mounting pressure to reshore production, AM offers more than just a workaround. It presents a fundamental shift in how we design, produce, and deliver products. From decentralizing supply chains to accelerating time-to-market, additive manufacturing is helping companies not just weather today’s storm, but future-proof their operations.
A New Trade Reality: Tariffs and Supply Chain Pressure
As of early 2025, newly imposed tariffs—particularly those targeting imports from China and other major manufacturing economies—are reshaping sourcing and procurement strategies across industries. According to U.S. Customs data, more than two-thirds of Chinese imports are now subject to higher duties, with additional tariffs extending to critical sectors like automotive components, electronics, and industrial equipment.
These measures have sent shockwaves through global supply chains, raising prices and lengthening lead times for manufacturers reliant on international suppliers. But even beyond China, geopolitical instability—from the war in Ukraine to tensions in the South China Sea—is pushing countries to reevaluate their industrial dependencies. Add to that inflationary pressures, persistent labor shortages, and residual post-pandemic logistics strain, and it’s clear that businesses need more resilient, localized, and cost-effective solutions.
Enter additive manufacturing.
1. Building Resilient Domestic Supply Chains
With tariffs driving up the cost of imported goods, manufacturers are looking inward—and AM is accelerating the shift toward domestic production. Unlike traditional manufacturing, which often requires complex, global sourcing of parts and raw materials, AM enables companies to produce finished components locally, using digital files and minimal physical infrastructure.
During the COVID-19 pandemic, this shift was already underway. Stratasys’ Origin® One P3™ printers were used to produce millions of nasopharyngeal swabs domestically, scaling up to 190,000 swabs per day when overseas supply chains failed. That response foreshadowed today’s reality: supply chain resilience isn’t a luxury, it’s a requirement.
Now, with tariffs compounding existing risks, more companies are investing in additive manufacturing to insulate their operations from external shocks. By decentralizing production, businesses can reduce dependency on international freight and raw material imports, protect against cost spikes, and improve supply chain visibility.
2. Mitigating Cost Pressures Through Efficient Production
The impact of tariffs isn’t limited to raw material costs—it also affects pricing competitiveness and margin control. Traditional manufacturing methods involve high setup costs, expensive tooling, and large minimum order quantities, all of which become harder to justify in a high-cost trade environment.
AM helps companies stay competitive by reducing material waste, eliminating tooling costs, and enabling low-volume production without sacrificing profitability. Northrop Grumman offers a compelling example. In its solid rocket motor program, the company adopted AM to replace traditional tooling used to mold propellant within motor casings. The result? Tooling lead times were slashed from months to weeks, and the company was able to iterate faster and at lower cost.
In an era when every dollar matters, additive manufacturing provides a leaner, smarter way to manufacture—one that aligns perfectly with the demands of a protectionist economy.
3. Reshoring with High Precision and Performance
While cost savings are a major driver of reshoring, industries like aerospace, medical, and defense also demand extreme precision and strict quality control. AM excels in these environments by enabling production of high-performance parts with complex geometries that traditional methods struggle to achieve.
A case in point: Spanish aerospace supplier Indaero used 3D printing to reengineer a critical assembly tool for an Airbus NH90 helicopter. The traditionally manufactured aluminum tool was heavy, difficult to handle, and time-consuming to produce. By switching to AM, Indaero delivered a tool that was nine kilograms lighter, reduced manufacturing time by 66%, and cut tooling costs by 50%.
As more companies look to bring production home in response to tariffs and trade volatility, AM makes it feasible—not just in theory, but in practice. The ability to produce specialized, flight-ready, or medical-grade components domestically is a game-changer for U.S. industry.
4. Reducing Logistics and Warehousing Burden with Digital Inventories
One of the less obvious consequences of global tariffs is the strain they place on logistics and warehousing. Higher import costs and port congestion force manufacturers to hold more inventory domestically, tying up capital and increasing overhead. Additive manufacturing turns this model on its head.
With digital inventory systems, companies can store product designs in the cloud and print parts on demand—eliminating the need for large physical stockpiles. This just-in-time approach saves money and space while allowing for greater responsiveness to market demand.
Fathom, a U.S.-based advanced manufacturing provider, illustrates this perfectly. As an early user of the Stratasys Continuous Build 3D Demonstrator, Fathom helped Intel produce more than 9,700 parts for “Spider Bots” featured at its developer conference. The project was completed in just five weeks—at a fraction of the traditional cost—demonstrating the power of AM to scale quickly without bloated inventory or production delays.
Fathom’s integration of AM into its operations reduced inventory by 93% and lead times by up to 75%, freeing up resources to focus on innovation and customer responsiveness.
5. Powering Innovation in a Protectionist Era
Trade restrictions often limit access to international partners, technologies, and suppliers. But that doesn’t mean innovation has to slow down. Additive manufacturing empowers companies to take control of their R&D and prototyping processes, enabling rapid iterations without external dependencies.
Instead of waiting weeks or months for overseas tooling or parts, engineers can now go from concept to prototype in a matter of days. That speed gives businesses a critical edge—not just in getting to market faster, but in being able to respond to customer feedback in real time.
In an economy defined by volatility, that kind of agility isn’t just nice to have—it’s essential
The Bottom Line
The new tariffs in 2025 are more than a policy change — they’re a catalyst for industrial reinvention. While the return to protectionism introduces new challenges, it also creates an opportunity to rethink how we manufacture, where we manufacture, and why.
Additive manufacturing stands out as one of the most effective ways to adapt. It supports domestic production, reduces exposure to global volatility, lowers operational costs, and unleashes a new level of design freedom. Whether you’re building aerospace components, healthcare devices, or industrial tools, AM helps you do it faster, smarter, and closer to home.
As manufacturers recalibrate for the realities of today’s trade environment, one thing is clear: additive manufacturing isn’t just a response to disruption — it’s a strategy for long-term growth and resilience.
About Stratasys
Stratasys is leading the global shift to additive manufacturing with innovative 3D printing solutions for industries such as aerospace, automotive, consumer products, and healthcare. Through smart and connected 3D printers, polymer materials, a software ecosystem, and parts on demand, Stratasys solutions deliver competitive advantages at every stage in the product value chain. The world’s leading organizations turn to Stratasys to transform product design, bring agility to manufacturing and supply chains, and improve patient care.
To learn more about Stratasys, visit www.stratasys.com, the Stratasys blog, X/Twitter, LinkedIn, or Facebook. Stratasys reserves the right to utilize any of the foregoing social media platforms, including Stratasys’ websites, to share material, non-public information pursuant to the SEC’s Regulation FD. To the extent necessary and mandated by applicable law, Stratasys will also include such information in its public disclosure filings.